Case Study: Sodium Silicate Spray Dryer Filtering using GORE® Filter Bags
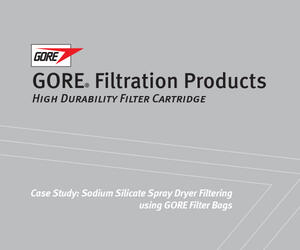
Case Studies, Englisch
Production goals met and exceeded without enlarging the baghouse. The bags have performed consistently well for the past 12 years, with scheduled changeouts every 24 months (although bag life has reached 30 months).
Application
One pulse jet baghouse (1,792 bags).
Optimization Potential
Restricted production rates - the existing baghouse was experiencing 7.5" H2O differentials with an air-to-cloth of 1.5/1 cfm/ft² and inlet grain loadings of 9.7 gr/acf with the fine, very hygroscopic dust. Differentials in excess of 7.5" H2O had caused the baghouse casing to collapse. Increased product throughput would require approximately a $1,000,000 US expenditure to enlarge the baghouse and require up to 24 months to appropriate the funds and complete the construction.
Solution
Installed GORE® membrane/NOMEX® felt filter bags.
Results
Production goals met and exceeded without enlarging the baghouse. The bags have performed consistently well for the past 12 years, with scheduled changeouts every 24 months (although bag life has reached 30 months). Since installation of the first set of GORE membrane filter bags, the product throughput has increased by better than 60%, the airflow increased 30% and the differential pressure has not exceeded 5.5" H2O. Even with one compartment off-line for maintenance, production rates can be maintained. Bags survived upsets and resisted contamination from carbon black as a result of fuel/air ratio malfunction.
FOR INDUSTRIAL USE ONLY
Not for use in food, drug, cosmetic or medical device manufacturing, processing, or packaging operations.